The lead engineer at a large refinery in California, part of one of the world's biggest oil corporations, faced the challenge of upgrading a fluid catalytic cracking unit in a short timeframe.
Having an accurate, current as-built of the existing facility was crucial to ensuring installation of the new unit without rework or project delays, but the complete dataset would need to be provided in just four weeks. The traditional approach of using pocket tape measures and asymmetrical sketches was out of the question.
Company
F3 & Associates
Location
Benicia, CA
Believing that 3D laser scanning was the only conceivable way to gather accurate and comprehensive plant documentation in such a short period, the engineer contacted F3 & Associates, a company that he knew was an expert in 3D scanning and modeling. Would they be able to help?
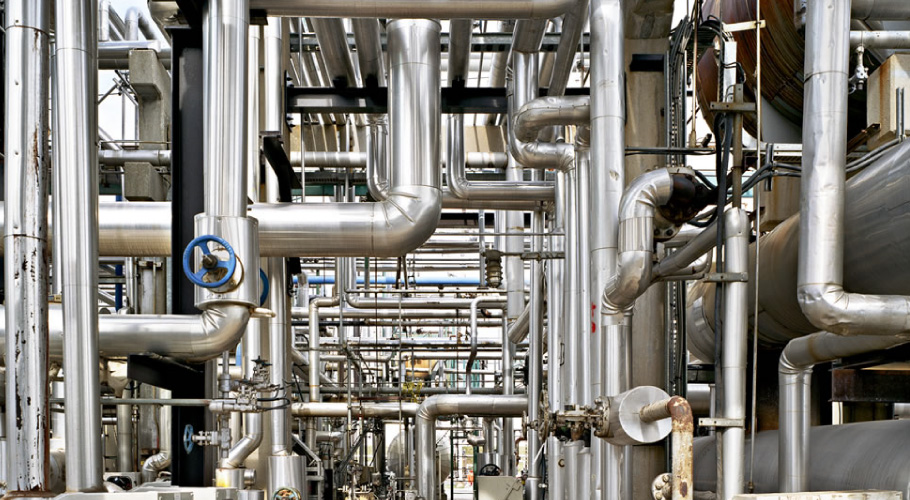
Technology, Teamwork and Creativity Make It Happen
The use of high resolution scans and photographs provides the richest possible data set to facilitate the most accurate planning.
Even with the assistance of 3D laser scanners, the team at F3 & Associates knew they would have to be creative to find a way to meet the deadlines. “We pride ourselves on being able to respond quickly, no matter how unrealistic the requirements may seem at first,” says Sean Finn, Principal, F3 & Associates. “In this case, we had to condense a project that would normally take two months into half the amount of time.”
To accomplish the goal, the team created a strategic workflow that used three Leica High Definition Surveying (HDS) laser scanners working concurrently. The firm already owned a Leica ScanStation C10, which captures up to 50,000 points per second and has a range of up to 300 meters; and a Leica ScanStation P20, which captures up to 1 million points per second at a range of up to 120 meters. Since time was of the essence, the firm rented one more Leica ScanStation P20 laser scanner and used the two high-speed scanners to capture most of the data. In areas that required long-range, high-elevation scans, the team used its Leica ScanStation C10.
“The combination of the two scanner types was great because we could get the C10 working for 45 minutes on a long-range scan while the P20s captured five more scans at the specified high-resolution requirements, plus took photographs,” says Finn. The use of high resolution scans and photographs provides the richest possible data set to facilitate the most accurate planning.
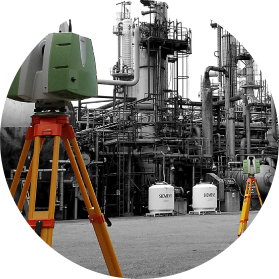
Five professionals from F3 & Associates compiled the data, some doing surveying ahead of the scanners to provide ground control while others operated the scanners. Because the team members had been cross-trained on surveying and scanning, they had some flexibility to help each other out to ensure that bottlenecks did not occur. For example, if the associates who were scanning caught up with the survey crew, they took a break from scanning and assisted with the surveying.
The Safer Solution
While the team was able to capture better information more quickly compared to traditional documentation methods, they also benefited from increased safety. Without laser scanning, they would have needed to use scaffolding and man-lifts to access hard-to-reach areas, but the Leica ScanStation P20 and C10 can document everything from the ground. In addition, because the data collected enables plant managers to plan installations methodically, it minimizes the amount of time that people have to spend in the plant. It’s not necessary, for example, to revisit the plant to fill in gaps in the data because the data the P20 collects is so rich. Finn notes, “The less time you spend in the facility, the safer the project.”
Keeping the Workflow Simple
Leica ScanStations are the standard in the petrochemical industry, but Finn said he also chose to use them because of the workflow simplicity. Once they captured the data, F3 & Associates downloaded it into the Leica Cyclone software, which allowed them to register the high accuracy point clouds quickly and easily. The associates then provided the refinery with a high resolution registered point cloud with photographs, as well as 3D prints for strategic areas to help stakeholders visualize the plant.
Tremendous Time Savings … and More
In the past, they would start with a long, shopping list of items to document.
Using traditional tools such as pocket tapes and a clipboard, a project of this scale would have taken about six months. Finn estimates that the use of Leica Geosystems’ laser scanners, plus their creative workflow, reduced documentation time to one month. However, he adds that without laser scanners, “I’m not sure it would even be possible.”
In the past, they would start with a long, shopping list of items to document. Then they would go onsite to tie out, for example, pipe rack elevations, anchor bolts and key structures that would show engineers where to start and where to end. The challenge, however, is to get from point A to point B. “How are you going to route that pipe? What are you going to miss?” says Finn. “With laser scanning, you can fabricate the pipe and know the route it’s going to take, the angle points required and where the touch points will be.
Laser scanning allows you to build things with more confidence.” And, of course, the engineers could see it all on their computers from the comfort of their offices.
Because the refinery obtained such a wealth of information within just a few weeks, they were able to save money on data collection and accurately plan the design, construction and installation of their new catalytic cracking unit, thereby avoiding unnecessary delays and downtime.
HIGH-VALUE DELIVERABLES
- High resolution registered point cloud
- Photographs
- 3D plastic prints
BENEFITS
Increased Safety
All data captured from ground level
Fast Data Collection
1 month vs. 6 months
Comprehensive Data Capture
Complete and accurate as-is dataset can be reused for future projects
Reduced Downtime
Perfect-fit installation means no rework
Better Project Visualization
3D models and 3D prints enable stakeholders to make better decisions