In the Gulf of Mexico, hundreds of production platforms and drilling rigs produce hundreds of millions of barrels of oil and gas equivalent. Deepwater platforms are particularly complex, tapping into oil buried at depths of 23,000 to 28,000 feet beneath the ocean surface. Retrofitting these structures can be a challenging task – especially when as-built documentation is incomplete or inaccurate.
Recent updates were not included, and details such as pipe insulation and cable trays less than 1 foot long were never documented.
Company
GIS
Location
Galliano, Louisiana
In 2014, one of these deepwater platforms began an expansion that involved drilling four new subsea wells, adding a subsea manifold to direct fluids from these wells into a single flowline, and tying it all into existing production headers. The project also required connecting a test riser and three production risers to the platform, as well as incorporating three new pig traps. Given the platform was already covered with a dense maze of piping, it was a complex engineering project made even more complicated by missing information in the CAD model. Recent updates were not included, and details such as pipe insulation and cable trays less than 1 foot long were never documented.
Capturing Every Detail with Accuracy
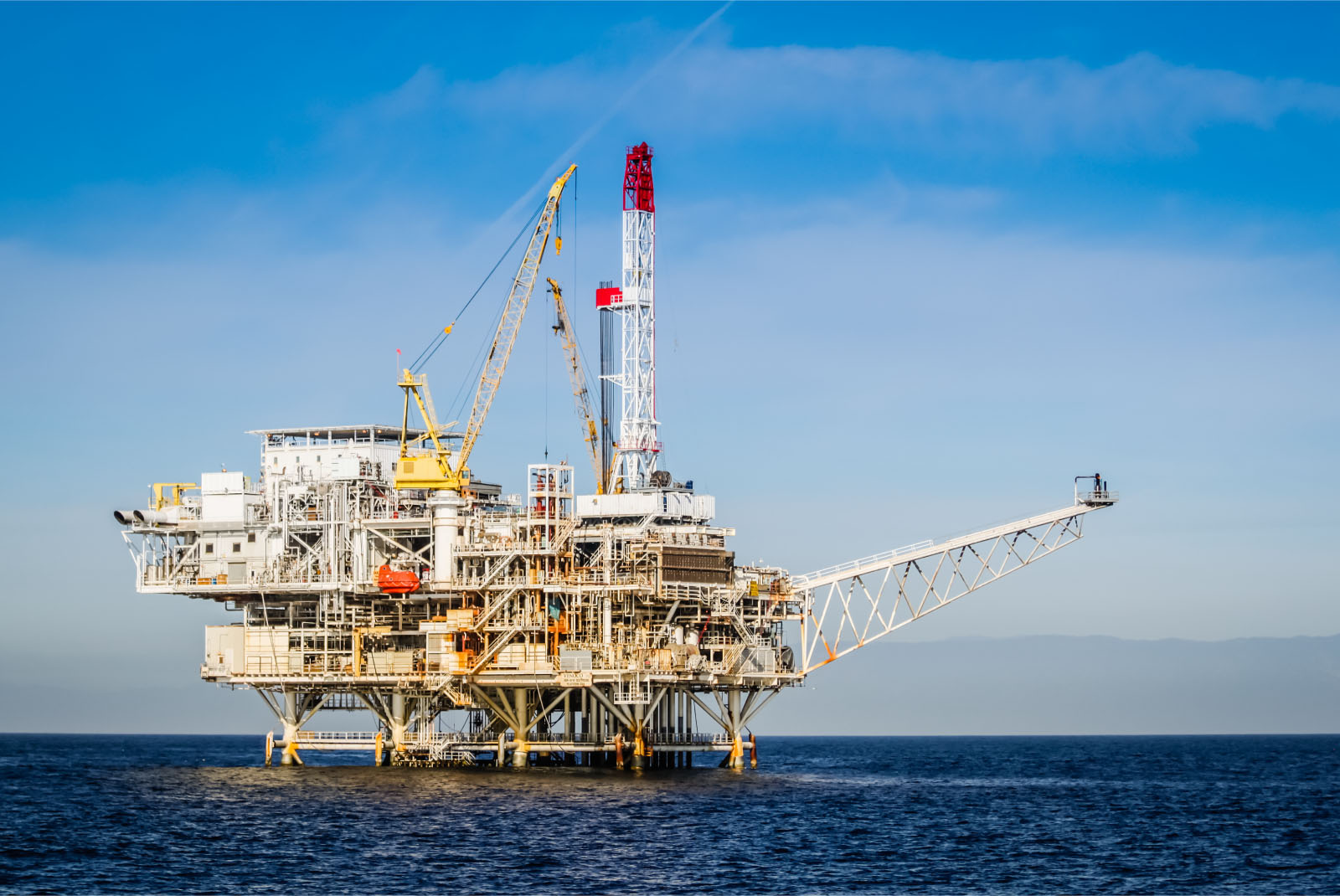
Laser scanning is ideal for amassing data on an oil platform topside because it records everything within its line of sight rapidly and accurately.
Recognizing that 3D laser scanning was the ideal way to capture as-is information on the platform, the project manager enlisted the support of GIS, a construction services company based in Galliano, La., that had previously conducted laser scanning for the corporation on another subsea development project.
Laser scanning is ideal for amassing data on an oil platform topside because it records everything within its line of sight rapidly and accurately. It uses a laser beam to determine the distance to objects and capturing a point cloud — a set of data points within a coordinate system. Because the laser records everything, the oil company would not need to build scaffolding or have workers don harnesses to climb the piping and take manual measurements.
Damian Craig, who now serves as senior project manager, drafting and laser scanning manager for the company, was initially dubious that the technology could rival his ability to take precise measurements.
Thus, laser scanning would save time, reduce safety risks, ensure accuracy and provide the comprehensive data required. Once captured, the point cloud would enable project engineers to ascertain measurements on the intricate structure, locate tie-in points, avoid clashes in their designs and ensure all parts fit together correctly.
Mark Pregeant, CEO of GIS, had invested in a Leica Geosystems 3D laser scanner in 2010 primarily to solve a labor problem. It was becoming harder to find and hire skilled offshore pipe fitters, and this technology would reduce the number of people needed on every job. Also, his clients could benefit from the high value deliverables it would enable the company to produce. Damian Craig, who now serves as senior project manager, drafting and laser scanning manager for the company, was initially dubious that the technology could rival his ability to take precise measurements. Soon, however, he became a convert due to the precise measurements it can capture and its ability to hold up to the environment and rough handling. “The accuracy of the Leica Geosystems laser scanner far exceeds anything else on the market, and it’s more robust too,” says Craig. “You need a sturdy instrument when you’re in an offshore environment because it has to withstand the effects of salt water, winds, rain. Also, we throw the scanner on a boat or in a personnel basket during transfers, so it has to hold up when it’s moved around.”
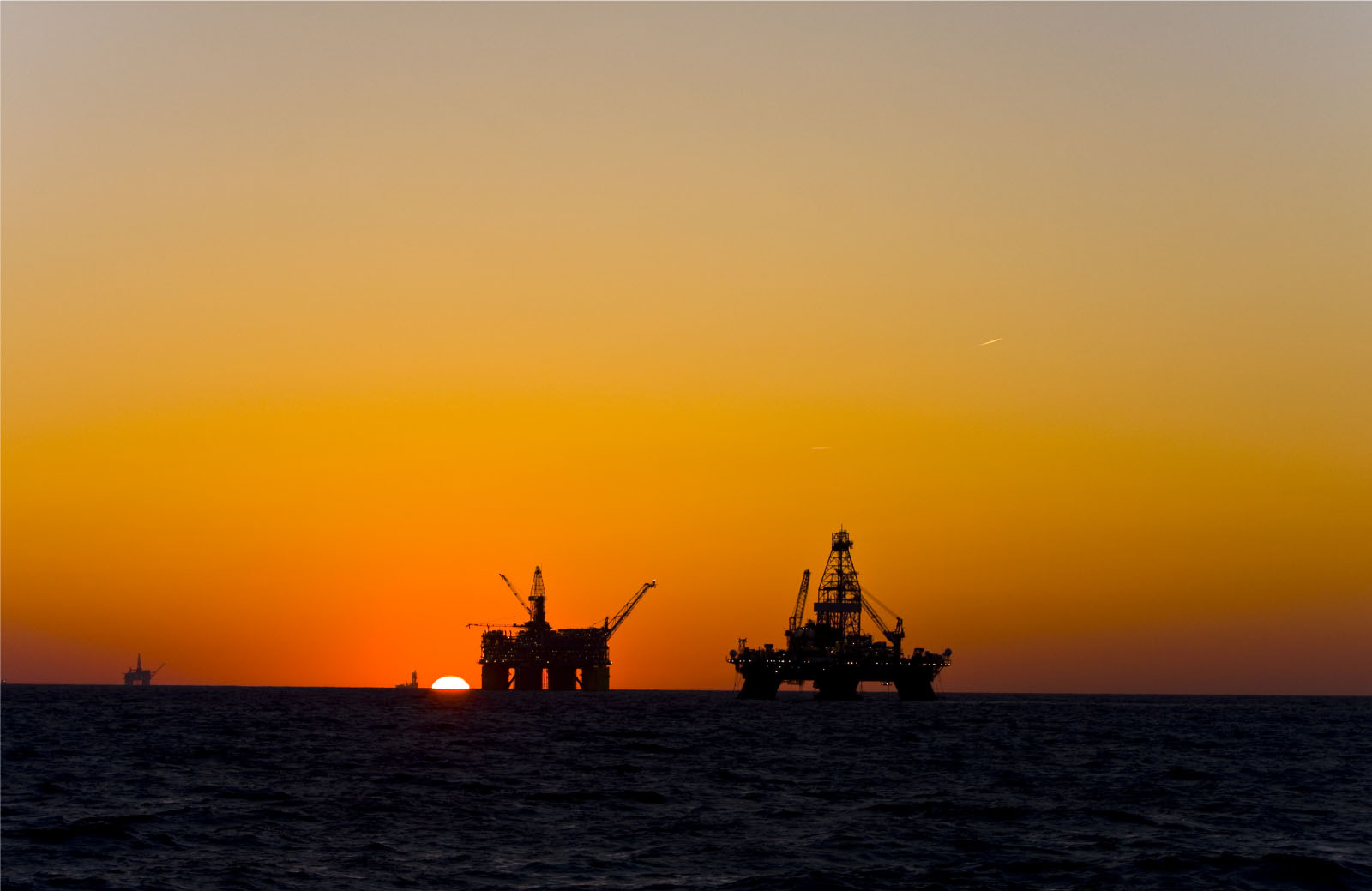
Minimizing Platform Downtime and Rework
GIS provided a seamless point cloud to the project engineers, which used it to ensure that their designs did not clash with existing construction and all new components fit perfectly.
GIS’s surveying task included scanning five decks which total approximately 139,000 square feet. It took the three-person crew four weeks to capture the data. The first week, they surveyed the platform and set up targets to aid in scan registration. Next, they captured 1,700 scans of the platform. GIS’s surveyors are unusual in that they are also draftsmen. Thus, they were able to collect data during daytime and assemble much of it at night. Their process included reviewing the scans at a low resolution see if any were compromised, for example, by someone walking in front of the scanner. If they were, the crew could rescan the area the next day, ensuring they had all the data needed. While doing drafting immediately after surveying required long days, 15 to 16 hours, it reduced project turnaround time.
After the crew returned to the office, post-processing took just 10 days. GIS provided a seamless point cloud to the project engineers, which used it to ensure that their designs did not clash with existing construction and all new components fit perfectly. In this way, the data collected minimized plant downtime and minimized rework.
Also, GIS engineers imported the data into Leica Cyclone software. They aligned and stitched together the point clouds captured from multiple positions, georeferencing the targets. This data, kept in-house, serves two purposes. First, after the project engineers created their drawings, they expected GIS to verify all the measurements. Engineers can safely and conveniently revisit the platform at any time on their computers to confirm measurements. “Instead of us having to put a tape measure on everything and check dimensions in the field, we can just take the engineers’ data and drop their model in our point cloud. In this way, we verify their work,” says Craig. With this data at their fingertips, GIS is also ready to assist on any additional maintenance or construction projects.
HIGH-VALUE DELIVERABLES
- High resolution registered point clouds
BENEFITS
Increased Safety
All data captured from ground level
Fast Data Collection
All data captured in four weeks, reducing project turnaround time
Comprehensive Data Capture
Complete and accurate as-is dataset minimized plant downtime and rework
Better Project Visualization
Seamless point clouds ensured that designs did not clash with existing construction and all new components fit perfectly