Using 3D laser scanning to capture existing conditions on secondary containment is a basic preventive measure that can provide a significant return on investment.
Tank inventory, tank condition, piping system condition – all these aspects of tank and terminal operations need to be regularly inspected and documented to comply with regulations, safeguard your site and protect your business. In the U.S., oil and gas facility owners and operators are required to comply with the Environmental Protection Agency’s (EPA) Spill Prevention, Control, and Countermeasure (SPCC) Regulation (40 CFR part 112), as well as the National Fire Protection Agency’s (NFPA) Flammable and Combustible Liquids Code (NFPA 30). Other countries have similar directives. But what is often overlooked in the documentation of oil, gas and chemical plants is the condition of the secondary containment structures.
Location
Crockett, Calif.
Section 112.7(c) of U.S. EPA 40 CFR notes, in part, “The entire containment system, including walls and floor, must be capable of containing oil and must be constructed so that any discharge from a primary containment system, such as a tank or pipe, will not escape the containment system before cleanup occurs.” The containment must be “appropriate” and designed to address the “most likely quantity of oil that would be discharged from the primary containment system.” The details regarding what type of structure is appropriate and whether it will work as intended is left to the design engineers and not often given much further consideration. Ideally, the secondary containment system will never be called upon to perform as designed.
Unfortunately, accidents can and do happen. Having accurate, comprehensive digital documentation of your secondary containment structures is a smart preventive maintenance strategy that can help you minimize risk and safeguard your operations.
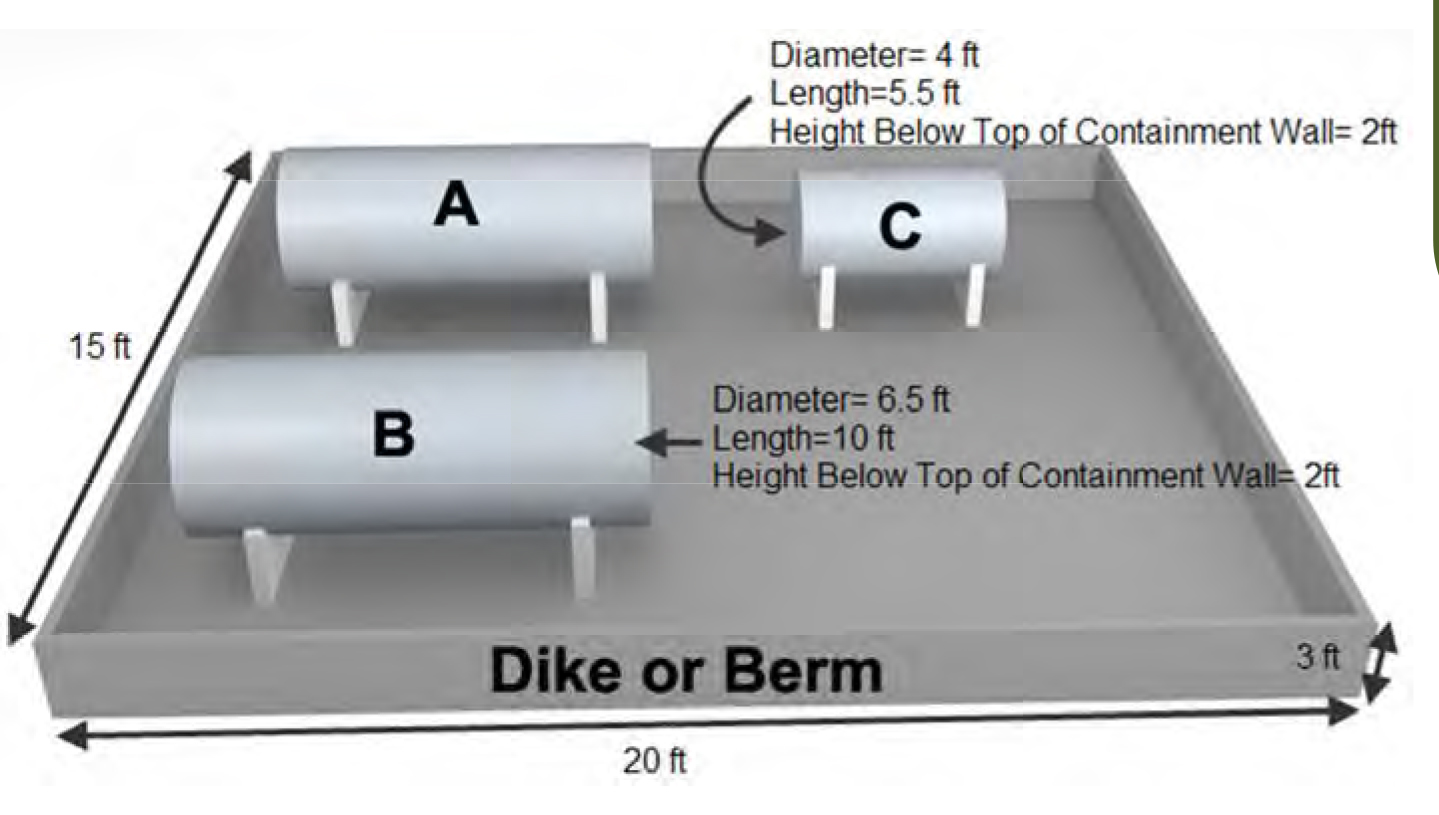
This diagram from an SPCC worksheet shows some of the measurements used to calculate secondary containment volume.
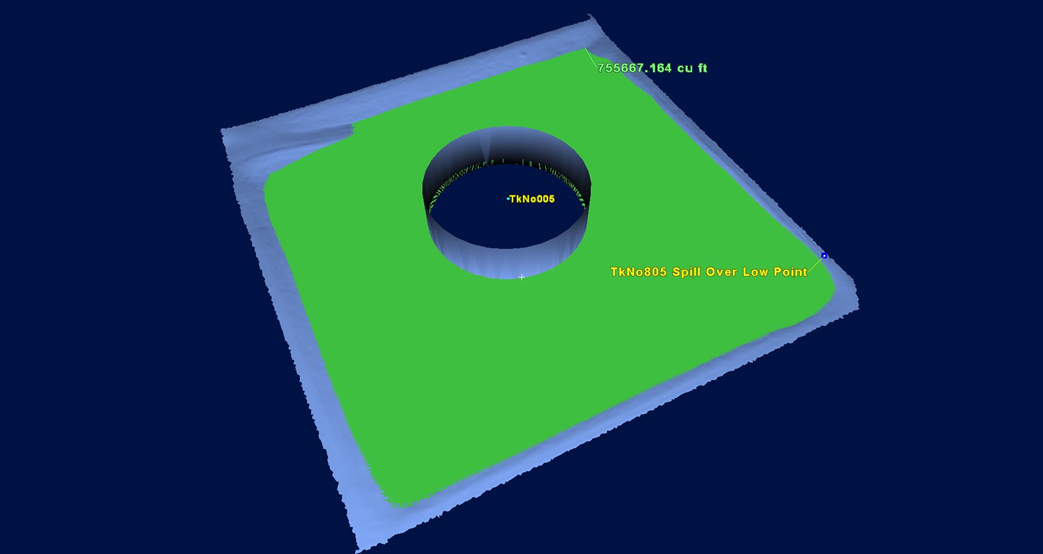
Accurate, comprehensive point cloud data captured with laser scanning provides valuable intelligence on capacity and spill scenarios.
Laser Scanning Quickly Pinpoints Problem Areas
Once you have the point cloud data, you can use it to create reports, calculate capacity, identify problem areas, manage operational risk, model spill scenarios and optimize efficiency.
In the past, facility owners and operators have had to rely on basic calculations to ensure they had the correct secondary containment volume. These calculations were based on measurements such as the largest tank shell capacity (based on tank diameter and length/width); secondary containment length, width and height; the height of each tank below the top of the containment wall; and the highest anticipated amount of rainfall. Traditional surveys using manual measurement methods, such as total stations, can capture some of this information in a simple tank farm but become less effective with increasing operational complexity, along with more stringent environmental and corporate safety guidelines.
D’Arcy Trask, president and founder of Gauge Point Calibration, Inc., based in Crockett, Calif., USA, has seen the limitations of traditional containment surveys firsthand. “You have to be able to answer the question, ‘If one of these tanks fails, is there enough containment to hold all of that volume?’” he says. “That question isn’t easy to answer in a facility with 40 or 50 tanks. There are also specifications for the grade from the tank to the toe of the wall or berm. If there’s a leak, it has to drain away from the tank shell and footing toward the wall or berm to avoid creating a fire or explosion hazard. Floor flatness, slopes and corner angles cannot easily be determined with traditional survey methods.”
Conversely, laser scanning captures every detail. A noncontact and nondestructive method of digitally capturing physical objects in 3D using a beam of light, or laser, laser scanning is a safe and accurate way to capture comprehensive as-built data in the form of a point cloud on entire tank and terminal operations, including secondary containment. Within the last several years, laser scanners have been developed that make it possible to capture clean, accurate 3D data with high dynamic range (HDR) imagery at an extremely fast scan rate of 2 million points per second. Having faster access to accurate, comprehensive data can mean the difference between making relatively minor preventive maintenance modifications and dealing with costly litigation.
“Laser scanning is a very powerful intelligence tool for facility owners and operators,” D’Arcy says. “Once you have the point cloud data, you can use it to create reports, calculate capacity, identify problem areas, manage operational risk, model spill scenarios and optimize efficiency. High definition surveying with 3D laser scanning is an enabling technology that delivers tremendous value.”
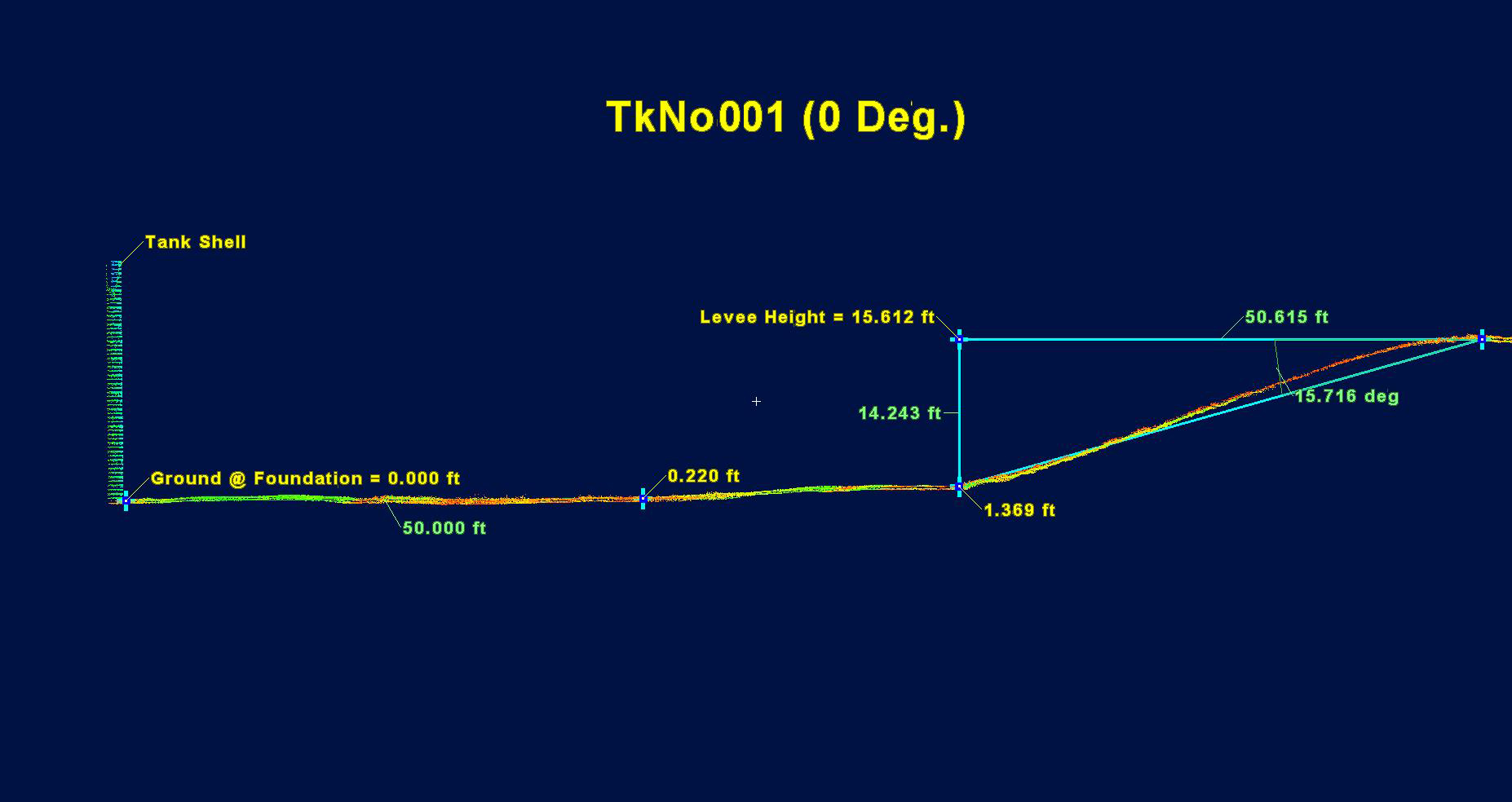
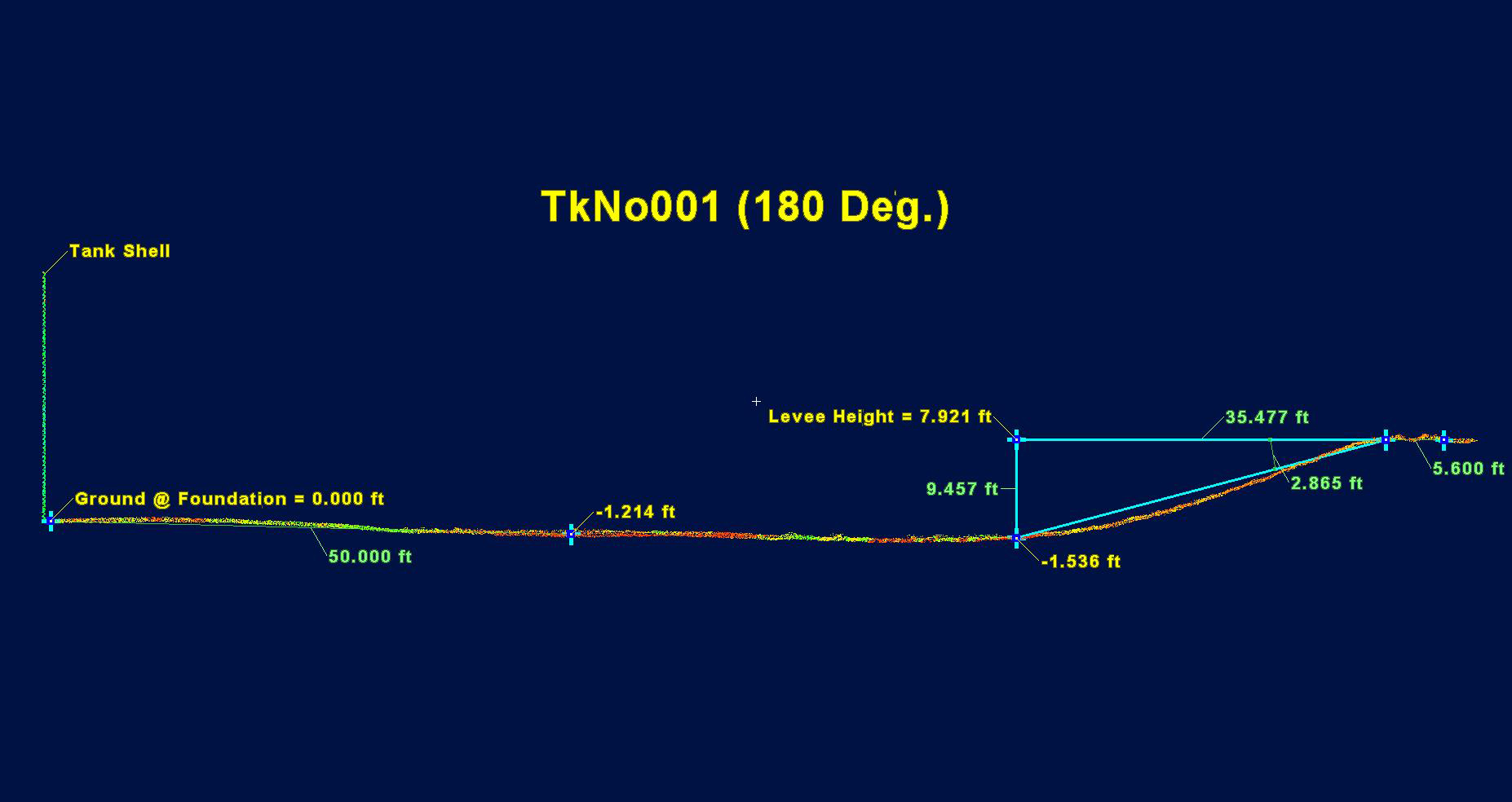

Laser scanning makes it easy to identify problems or low points that need to be corrected in the grade from the tank to the toe of the containment structure.
Laser Scanning Provides an Accurate Digital Record
Laser scan data is accurate, comprehensive, visual and easily accessible. It gives you peace of mind that you have all the information you need.
Gauge Point Calibration has been calibrating storage tanks for 28 years and has done work for every major oil company in the United States as well as the U.S. Navy on both underground and above ground facilities. Fourteen years ago, the company began using high definition 3D laser scanners from Leica Geosystems to capture tank data. “Leica Geosystems laser scanners are the standard in the industry and are known for their uncompromising accuracy and seamless workflows,” D’Arcy says. “Adding this capability to our expertise in tank calibration and surveying enabled us to provide a whole new level of service to our clients.”
In addition to providing basic calibration reports to the API MPMS 2.2D standard, the company helps clients manage operational risk and monitor for damage, overfill and environmental levels to meet the API 2350 standards. It performs conceptual design and interference checks, and it helps clients conform to API standards 650 and 653 for maintenance and inspection.
Importantly, laser scanning allows Gauge Point to provide information in an easily accessible, highly visual format. If a picture is worth a thousand words, a scan is worth a million words—or more. “As soon as our clients see the point clouds and 3D models from our laser scans, they immediately understand the value,” says John Barrella, Gauge Point’s Gulf Coast Regional Manager.
Although most of the company’s work has focused on tanks and piping systems, D’Arcy has noticed a growing demand for high-definition secondary containment surveys, especially for facilities located near waterways and other environmentally sensitive areas. Some facilities are trying to be more proactive as a matter of corporate responsibility. For others, news of explosions and secondary containment failures have been a wake-up call.
“When a major incident occurs at an oil and gas or chemical facility, agencies immediately shut the facility down, and investigators completely disassemble the tank and terminal operations looking for answers,” D’Arcy says. “Having an accurate, comprehensive digital record can serve as a critical resource for both owners/operators and investigators.”
The data can also provide crucial intelligence to first responders in an emergency by giving them detailed virtual access to the site before they arrive on scene.
While that’s a worst-case scenario that most facility owners and operators hope they never have to face, the data is useful in myriad other ways. For example, after a traditional survey indicated a potential containment capacity shortage at an oil and gas facility, the owner contracted Gauge Point to resurvey the facility with 3D laser scanning. Gauge Point’s high-definition surveys and digital data models proved the secondary containment was sufficient, saving the facility hundreds of thousands of dollars in unnecessary renovation costs.
The point cloud data also has long-term value, especially when laser scanning is used to capture entire tank and terminal operations. If future facility modifications are needed to add capacity or improve efficiency, owners and operators can return to the point cloud dataset to minimize or even eliminate the need for additional site surveys.
“Once you scan your facility and have that model, the data is invaluable,” D’Arcy says. “You no longer have to worry about not having incomplete or inaccurate documentation. Laser scan data is accurate, comprehensive, visual and easily accessible. It gives you peace of mind that you have all the information you need.”