The need to improve safety is driving many tank owners and operators to re-evaluate their tank gauging and calibration methods. D’Arcy Trask, founder and president of Gauge Point Calibration, Inc., explains how reality capture with 3D laser scanning is the preferred approach because of its ability to safeguard workers, facilities and surrounding communities.
High-definition 3D laser scanning is becoming widely recognized as the standard for storage tank calibration and maintenance. One reason is its ability to generate accurate strapping tables, helping facilities maximize working capacity and minimize risks. Even more important, however, is the enhanced safety provided by the technology.
Location
Crockett, Calif.
A noncontact and nondestructive method of digitally capturing physical objects in 3D using a beam of light, or laser, 3D laser scanning captures millions or even billions of measurement points on a tank’s surface. These combined points are known as a point cloud—a clear and precise digital record of the tank. This data can be used to generate basic calibration reports to the API MPMS 2.2A and D standards, manage operational risk and monitor for damage, overfill and environmental levels to meet the API 2350 standards, and perform conceptual design and interference checks to conform to API standards 650 and 653 for maintenance and inspection.
Instead of balancing precariously on lifts, ladders and tank ledges to collect tank data with poles and measuring tapes, workers can capture almost all the data they need from safe locations on the ground. What’s more, the data is comprehensive and actionable, giving decision-makers extraordinary insight into the tank’s condition and capacity. The implications for safety are significant.
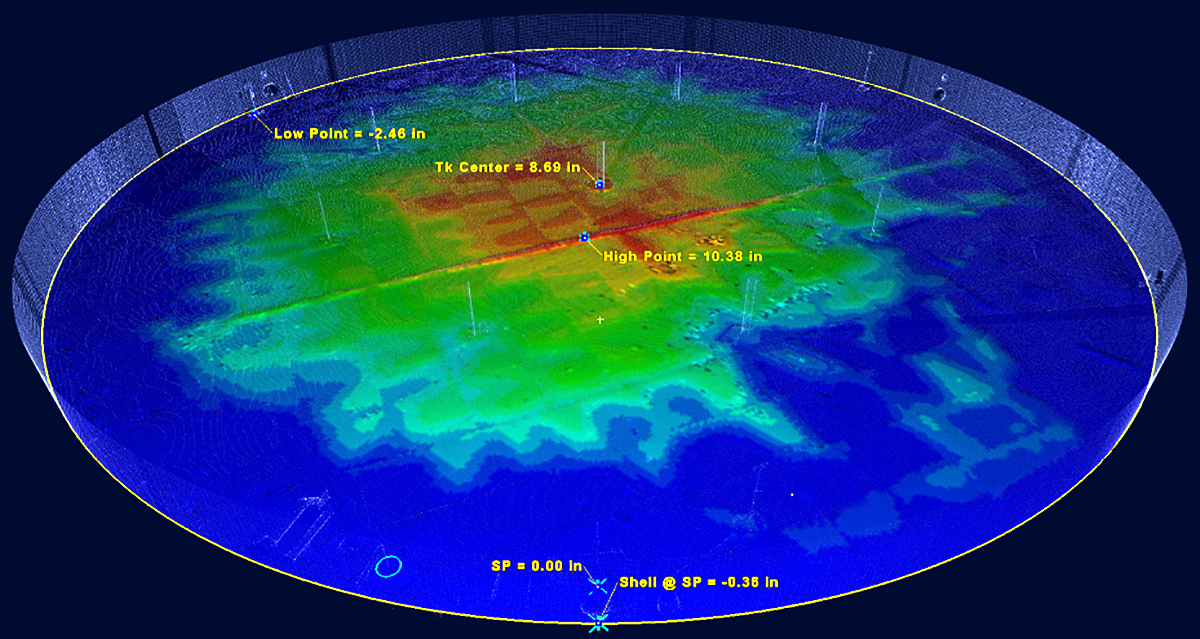
The high level of data density captured with 3D laser scanning allows any tank issues to be identified at a glance.
Less Time in the Tank
With 3D laser scanning, workers capture complete information on in-service tanks while minimizing their exposure to hazardous fumes and confined spaces.
Manual tank gauging is a risky endeavor. Between 2010 and 2014, the U.S. National Institute for Occupational Safety and Health (NIOSH) and Occupational Safety and Health Administration (OSHA) reported nine fatalities associated with tank gauging and sampling operations in the oil and gas extraction industry. Many of these deaths were attributed to exposure to hydrocarbon vapors and low oxygen environments. Minimizing or eliminating these exposures is imperative.
With 3D laser scanning, workers capture complete information on in-service tanks while minimizing their exposure to hazardous fumes and confined spaces. The long-range capabilities and exceptional data quality of professional-grade laser scanners such as the Leica ScanStation P-Series, combined with the advanced inspection and reporting capabilities of the Cyclone 3DR software, enables even tall cylindrical, round and irregular tanks to be captured effectively from the ground.
When interior data is needed on an out-of-service tank, data can be collected by a single person in a matter of minutes, minimizing the number of workers who need to be in the tank and the amount of time they need to spend in that environment. In many cases, interior data can be captured from the top of the tank by inverting the laser scanner, which avoids the need to enter the tank. Using laser scanning also reduces the potential for head bumps, eye-hand injuries, lifting injuries, trips and falls, and other injuries associated with manual tank gauging.
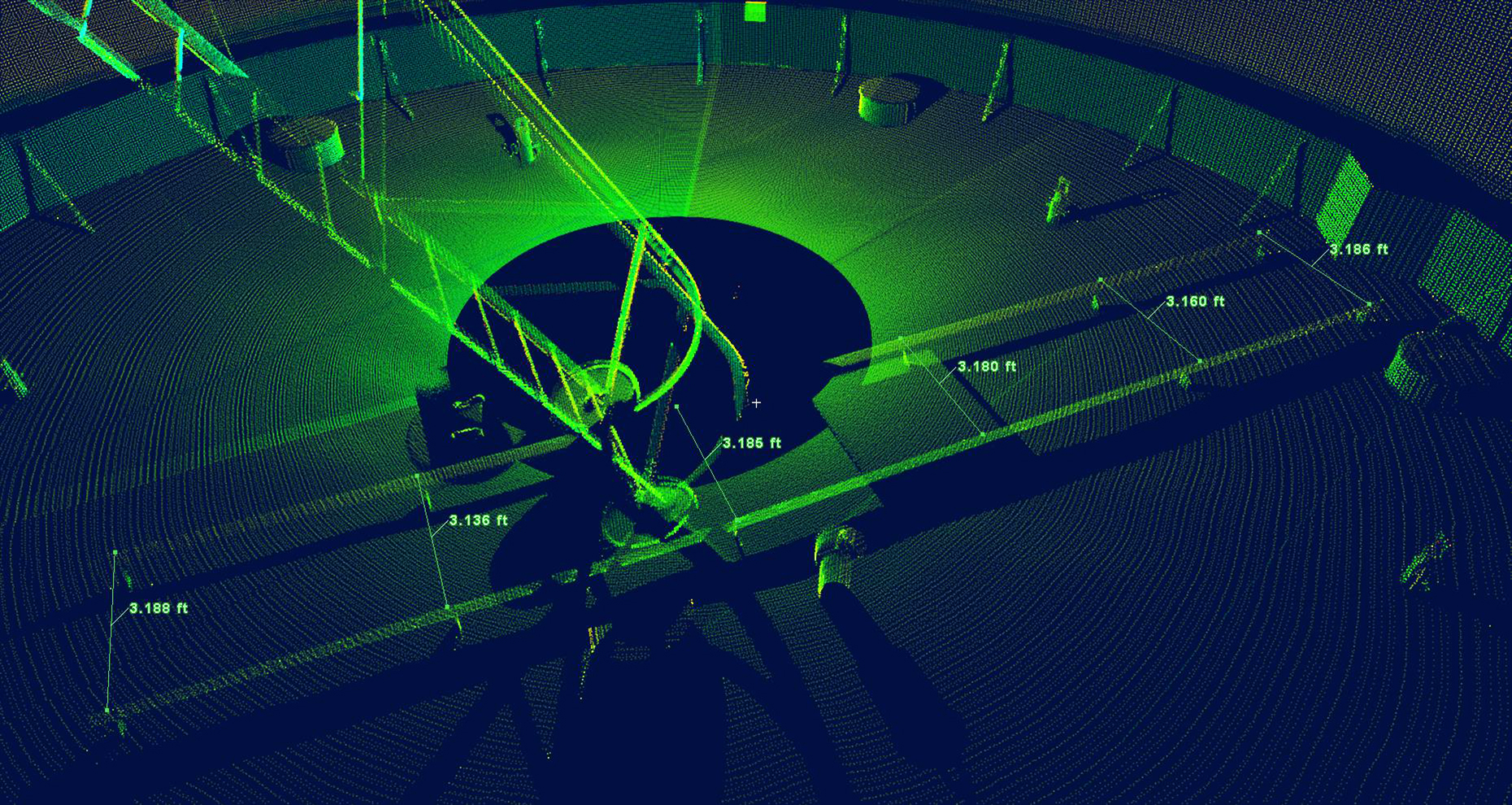
The data captured with 3D laser scanning revealed a hump in the tracking system for this rolling ladder, which was preventing the ladder from moving correctly.
Reduced Need for Fall Protection
Laser scanning keeps workers out of harm’s way while providing the reach to capture data wherever it’s needed.
Safety harnesses, fall and rescue devices, and confined space entry systems are all standard personal protective equipment (PPE) for tank calibration and maintenance personnel. But these systems require proper and consistent use to keep workers safe. A better approach is to eliminate the hazards and minimize the need for PPE by using 3D laser scanning.
Laser scanning keeps workers out of harm’s way while providing the reach to capture data wherever it’s needed. The data can then be brought back to the office in a 3D environment to obtain measurements and generate reports that wouldn’t even be possible with manual methods due to the risk of inaccurate or incomplete data.
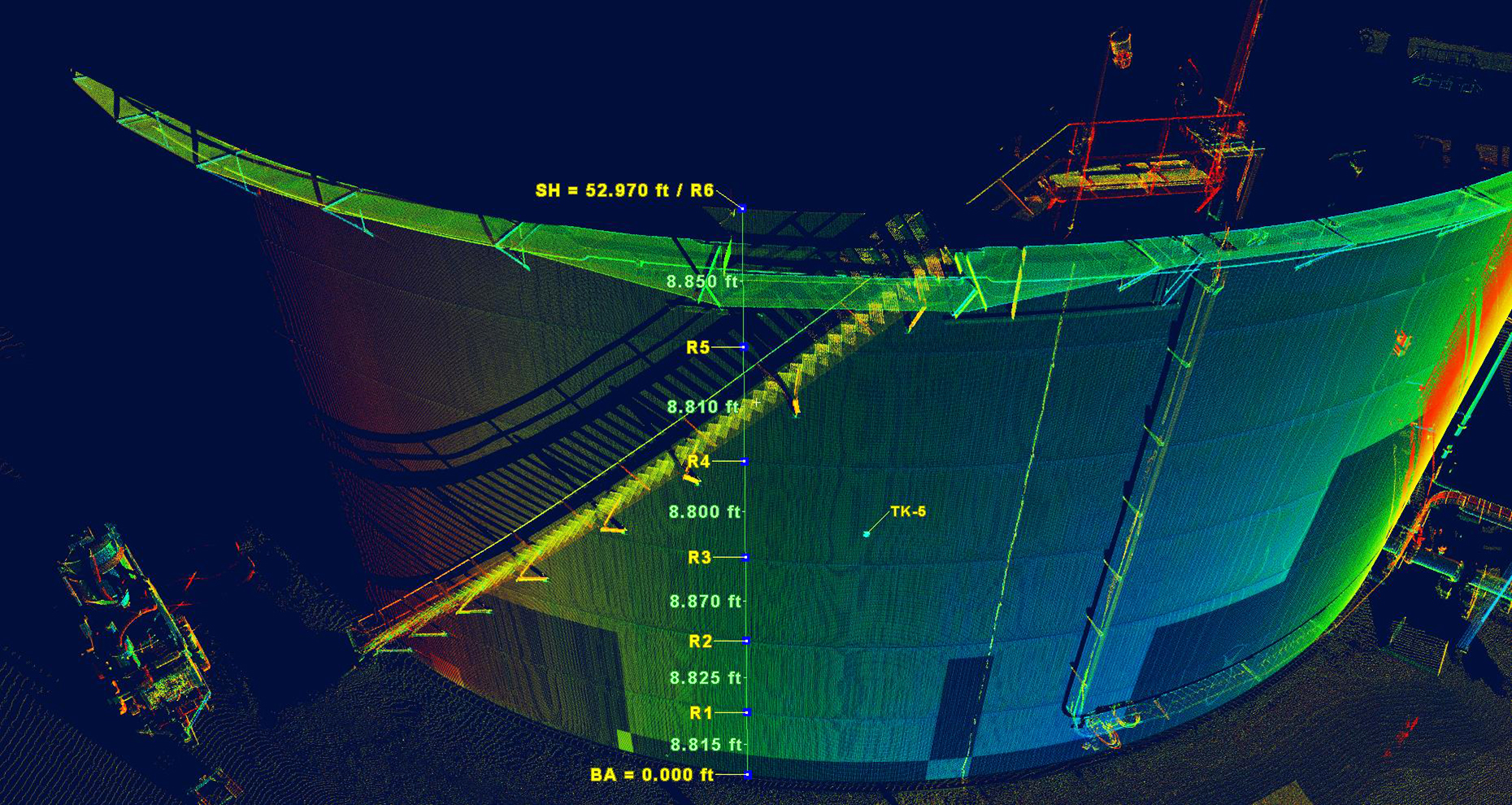
Laser scanning keeps workers out of harm’s way while providing the reach to capture data wherever it’s needed. The data can then be brought back to the office in a 3D environment to obtain measurements and generate reports that wouldn’t even be possible with manual methods due to the risk of inaccurate or incomplete data.
Improved DOE and Alarm Level Management
The amount of data collected with laser scanning, combined with the easy accessibility and visual format of the reports, provides accurate and actionable information.
In addition to safeguarding workers, 3D laser scanning provides an important advantage in protecting facilities and local communities by making it easy for tank owners and operators to determine safe operating limits. The amount of data collected with laser scanning, combined with the easy accessibility and visual format of the reports, provides accurate and actionable information on the damage, overfill and environmental (DOE) level of a tank to API 2350 standards so the tank can work at maximum capacity with minimum risk.
Laser scan data is so comprehensive that an experienced high-definition-surveying firm can determine overfill levels to within a couple hundredths of a foot. That kind of detailed information could never be obtained with manual methods or other electro-optical measurement methods, like total stations.
The data also provides a visual way to evaluate tank condition. Instead of relying on individual measurements, which could miss important information, reports based on laser scan data capture every aspect of the tank with subcentimeter density. This level of data density allows any damaged areas, weak points and edge settlements to be identified at a glance, so steps can be taken to correct potential problems before failures, leaks or explosions occur.
Better Comparative Data
Point clouds can be compared to original as-builts or older scan data to identify areas of deformation before they cause problems, reducing risk and repair costs.
The safety aspects of laser scanning extend beyond the initial data capture and reporting. Having access to comprehensive point cloud data captured for tank calibration or maintenance can minimize or eliminate personnel exposure to the tanks if future facility modifications are needed since the original data can often be used in engineering and design. Point clouds can also be compared to original as-builts or older scan data to identify areas of deformation before they cause problems, reducing risk and repair costs.
If an incident does occur, scan data can be used to support the investigation and identify the cause of the failure so preventive measures can be implemented.
As tank owners and operators search for ways to improve safety in tank calibration and maintenance, high-definition 3D laser scanning performed by an experienced service provider is increasingly recognized as the preferred method. It’s an investment that pays dividends in providing accurate, accessible, visual and actionable information both today and well into the future.