Today, we know where everything is, and now we’re really starting to understand how to leverage that information.
Plant expansions, modifications and retooling should be efficient and seamless. Unfortunately, many facilities experience the exact opposite. Existing as-built data is often incorrect or missing, leaving designers and engineers to fill in the gaps as best they can and revise the plans as they go along. Delays and rework are common, and the downtime is costly. General Motors recognized this challenge more than a decade ago and took visionary steps to transform its processes. The company hired experts in 3D laser scanning to capture comprehensive digital data on its facilities and create robust CAD models that could be used as the basis for engineering design. The value of the accurate and detailed models was immediately evident; over time, the designers and engineers also began to see tremendous value in the underlying point cloud data. “GM had a very focused reason for bringing us in: They didn’t understand where their stuff was,’” says John Brown, who led some of the earliest laser scanning work at GM and now serves as GM Reality Capture Supervisor. “Today, we know where everything is, and now we’re really starting to understand how to leverage that information.”
Company
General Motors
Location
Global
Laser Scan Data Drives Plant Safety and Efficiency
A key benefit of laser scanning is its ability to quickly and safely capture accurate, comprehensive measurement data. With the leading-edge Leica RTC360 laser scanner, billions of points of clean, dense data can be captured in the field in minutes and registered onsite, making it fast and easy to collect every detail of the facility, from the location of furniture down to the anchor bolts in the floor.
Being able to better plan things—whether it be a model changeover for vehicles, maintenance issues on the buildings or emergency response in a large facility—is very powerful.
This level of intelligence enables reality capture teams to answer critical questions and solve problems before they occur. “Facility modifications need to be done as safely, quickly and efficiently as possible,” John says. “We can come into an environment and answer questions designers and engineers don’t even know they have yet. We can predict the impact of a piece of equipment and identify potential problems prior to installation. We’re actually capturing everything we can see that’s out of reach. The Safety Group has become one of the big advocates for using the technology in the plant because it helps them understand how to keep people out of potentially hazardous situations.
“Being able to better plan things—whether it be a model changeover for vehicles, maintenance issues on the buildings or emergency response in a large facility—is very powerful,” he adds.
RELATED: Advancing the Digital Twin in Automotive Manufacturing
Accurate Point Clouds Promote Better Design and Engineering
Dense, accurate point cloud data is also useful outside of the plant. New equipment can be prefabricated offsite with confidence that it will fit perfectly as designed. Tooling companies can use the facility data to optimize solutions for the available space. “Suppliers can come to us and ask for point cloud data on a specific zone in a plant,” John explains. “For example, maybe they need to understand the wheel installation zone in general assembly. We can quickly pull that data and hand it off to them.”
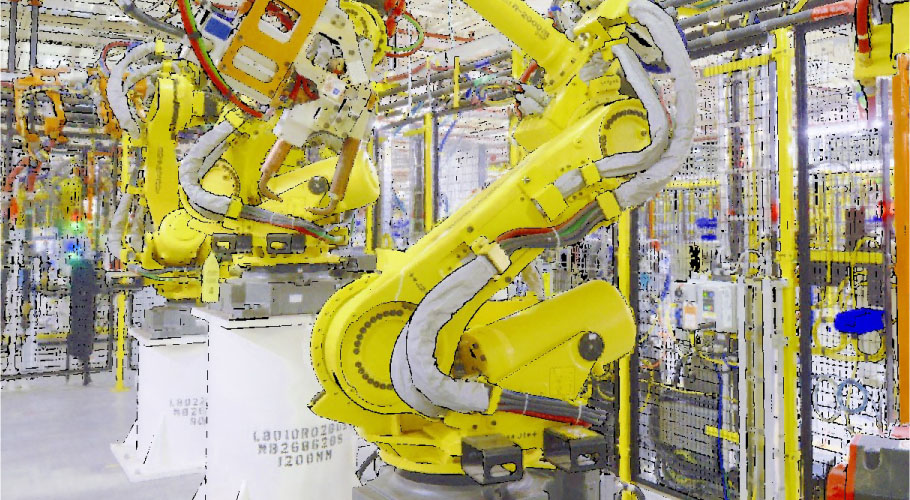
With laser scanning, teams can capture 3D spatial data on an entire facility and create a comprehensive data library that can be accessed as needed.
The availability of point cloud data, in turn, generates more demand. “The fact that they’re coming to us and requesting this raw data means they’re leveraging it for their engineering and design purposes, which shows the value in this information,” John says.
Easy Access to Comprehensive Spatial Data Advances Intelligence
With a greater understanding of the value of reality capture and the evolution of high-speed, easy-to-use hardware and software, plants are changing the way they collect, manage and apply the data. Instead of scanning a limited space for a specific project, teams can now capture 3D spatial data on an entire facility and create a comprehensive data library that can be accessed as needed. “The equipment is so fast now that it’s easy for us to collect everything,” John says. “And with the advances in software like Leica Cyclone, JetStream and CloudWorx, we have the ability to quickly turn it around to anyone who needs it and provide more insight that benefits the entire process.”
The point cloud data creates an ‘Aha!’ moment. Suddenly they’re seeing the whole environment and all the different things they might be able to do.
Engineers trying to install a new valve body line, for example, can easily check the point cloud to see whether it will fit in the existing space. But they can also use the point cloud to get significantly more visibility into that part of the plant, such as the location of drain lines and potential issues with floor flatness. “It’s kind of an ‘Aha!’ moment,” John says. “Suddenly they’re not looking down a line through a straw anymore but seeing the whole environment and all the different things they might be able to do. It’s exciting to see that shift taking place.”
Reality Capture Delivers a True Digital Twin
Manufacturing is the ideal proving ground for the digital twin—a digital replica of physical assets and processes that drives high performance by maximizing transparency and control. But a true digital twin can only be achieved with accurate reality capture at its core. “We might someday get to the point where a piece of equipment can reconcile itself in space. Maybe a robot that is moved in a plant will one day be able to calculate where it is relative to where it was and then transfer that information and update that CAD model on the fly,” John says. “Until that happens, we have to be able to accurately document where things move and how they change. Reality capture is imperative.”