Recent advances have made 3D laser scanning the fastest, most accurate and safest way to capture comprehensive tank data in the oil, gas and chemical industries. Joel Hurt, vice president of industrial plant solutions in the U.S. and Canada for Leica Geosystems, part Hexagon, explains why you should apply the technology throughout your terminal for even greater benefits.
It’s 3 a.m. on a Sunday, and you’re awakened by an alarm. A quick glance at your phone on your bedside table shows a critical situation at your plant: A flange bolt in the terminal has come loose due to vibration, threatening a major release of propylene. You calmly tap a few links, quickly identify the precise location of the bolt on a 3D map, and share the data with the night maintenance supervisor. With immediate access to clear and accurate information, the maintenance engineer tightens the bolt and resolves the problem, avoiding a disaster.
This scenario is just a glimpse of what’s possible in oil, gas and chemical plants as 3D laser scanning technology turns the idea of a digital twin into a reality. Across the industry, companies have already begun using 3D laser scanning to reduce risk, improve calibration and streamline maintenance on storage tanks. Forward-thinking firms are moving beyond tanks and applying the same technology to their entire operation as part of a standard operating procedure that gives them critical intelligence on every aspect of their facility. Here are three ways 3D laser scanning can be used to create a competitive advantage.
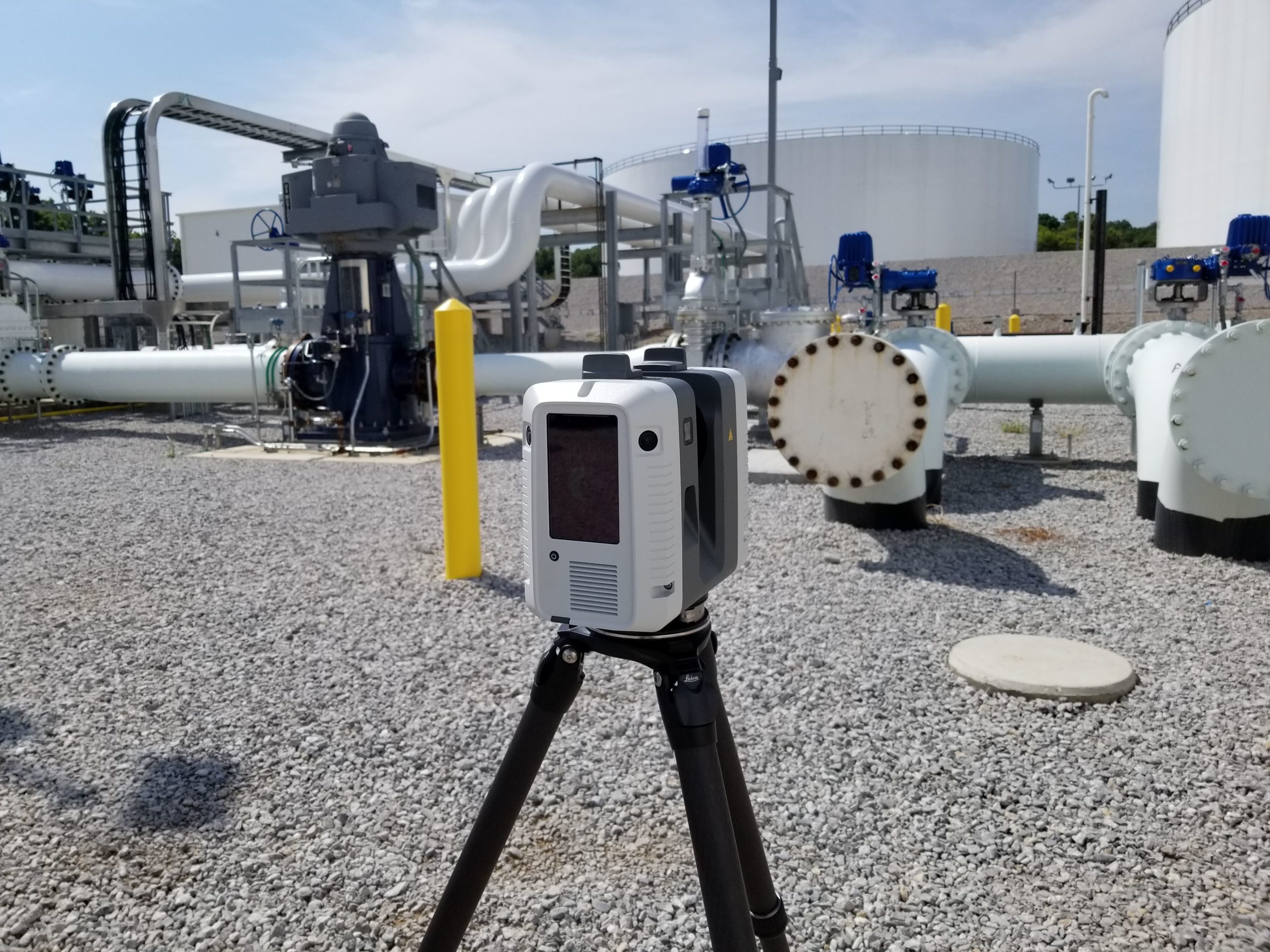
1. Accurate point clouds advance operational flexibility.
Any required changes or maintenance can be handled quickly and accurately using readily accessible measurement data.
A digital twin based on 3D laser scanning reality capture includes an accurate, comprehensive set of data points known as a point cloud that can be used in tank farm automation to ensure the most effective oil, gas or chemical movement and understand inventory in real time. Any required changes or maintenance can be handled quickly and accurately using readily accessible measurement data, which minimizes or eliminates downtime due to errors or rework.
2. Comprehensive data captured from a distance maximizes safety.
Instead of donning harnesses, climbing ladders, or erecting and balancing on scaffolding, personnel can quickly capture all the data they need from safe locations on the ground.
3D laser scanning is a non-contact and nondestructive method of digitally capturing physical objects in 3D using a beam of light, or laser. Within the past several years, laser scanners have been developed that make it possible to capture clean, accurate 3D data with high dynamic range (HDR) imaging at a fast scan rate of 2 million points per second. Software advances have made working with point clouds fast and easy, even when integrating point cloud data into existing CAD workflows. Instead of donning harnesses, climbing ladders, or erecting and balancing on scaffolding, personnel can quickly capture all the data they need from safe locations on the ground.
In addition to enhancing the safety of workers, 3D laser scanning improves the overall safety of plant operations. 3D visualizations based on accurate laser scan data enable plants to predict and visualize areas of potential hazards, including dents, cracks, corrosion, and strain, as well as track parameters responsible for risks to integrity. This type of intelligence improves overall risk management and minimizes the potential for losses.
3. Digital plant assets promote profitability.
Having a digital twin for both projects and assets can help you identify opportunities for improvement in process and design as well as asset management and performance.
Comprehensive and up-to-date inspection records are crucial for environmental compliance in the oil and gas industry and are probably already part of your Spill Prevention, Control and Countermeasure (SPCC) plan. But having a fast, easy and accurate way to create these records can also drive down the cost of maintenance and future modifications, both on your tanks and throughout your terminal operations. According to a recent report from Deloitte Insights, a digital data-driven approach can potentially reduce annual downtime by 70 percent and bring down unplanned cost to 22 percent of the total, compared to 50 percent currently. Having a digital twin for both projects and assets can help you identify opportunities for improvement in process and design as well as asset management and performance.
3D laser scanning is the fastest, most accurate and safest way to capture comprehensive digital data, making it easy for you to transform your operations. The future of digital is now. Are you ready?