Each time project managers have carved out space for the equipment and related piping, the plant has become more congested and complex.
With the capacity to slice 22,000 tons of beets a day and produce over one billion pounds of sugar annually, the Michigan Sugar Co. is the third largest sugar producer in the United States. Its factories, which were built between 1889 and 1902, dot the Michigan landscape, providing employment to many people. During peak processing season, more than 1,000 grower-owners and 1,600 workers support the company. Over the decades, Michigan Sugar has installed an assortment of machinery updates and additions in its Croswell, Michigan plant. The company has also augmented operations with auxiliary buildings that house new machinery. Each time project managers have carved out space for the equipment and related piping, the plant has become more congested and complex. Until recently, as is typical in many factories, plant documentation had not kept pace with the ever-changing environment.
Company
3D Imaging Services
Location
Flint, MI
Planning for a Tank Replacement
When Michigan Sugar Co.’s management decided to replace an evaporation tank that spans three stories inside the factory, the project engineer, Chris Schanbeck, knew careful planning was in order. In the past, to design the new structure and guide a project plan, his team might have updated old drawings of the facility with hand measurements of the planned installations. He knew, however, that inaccuracies and omissions in the as-built data could lead to unexpected equipment clashes and misfitting parts. The result would likely be field rework, increased costs and project delays.
To ensure a sound design, Schanbeck needed a comprehensive, accurate, up-to-date as-built model of the interior of the factory that would provide guidance for fabricating systems and components for the new tank and its structural steel support. A comprehensive model would also enable the team to plan how to move support equipment, such as pumps and piping, that was required to install the new tank. And it would allow designers to model how best to re-route and connect the labyrinth of piping after installing the new tank.
When Schanbeck researched his options for creating such a model, a colleague referred him to 3D Imaging Services in Flint, Mich. The company provides technology solutions that include 3D laser scanning and as-built modeling. Schanbeck believed their 3D laser scanning capabilities would allow Michigan Sugar to produce the most precise, detailed model possible. Michael James, project manager at 3D Imaging Services, headed up the project. “Because the project was already in the planning phase and Michigan Sugar needed a way to capture existing conditions rapidly, time was of the essence. Because of this, we chose the Leica ScanStation P40 to document the plant. It enabled us to reduce both field time and processing time,” he says.
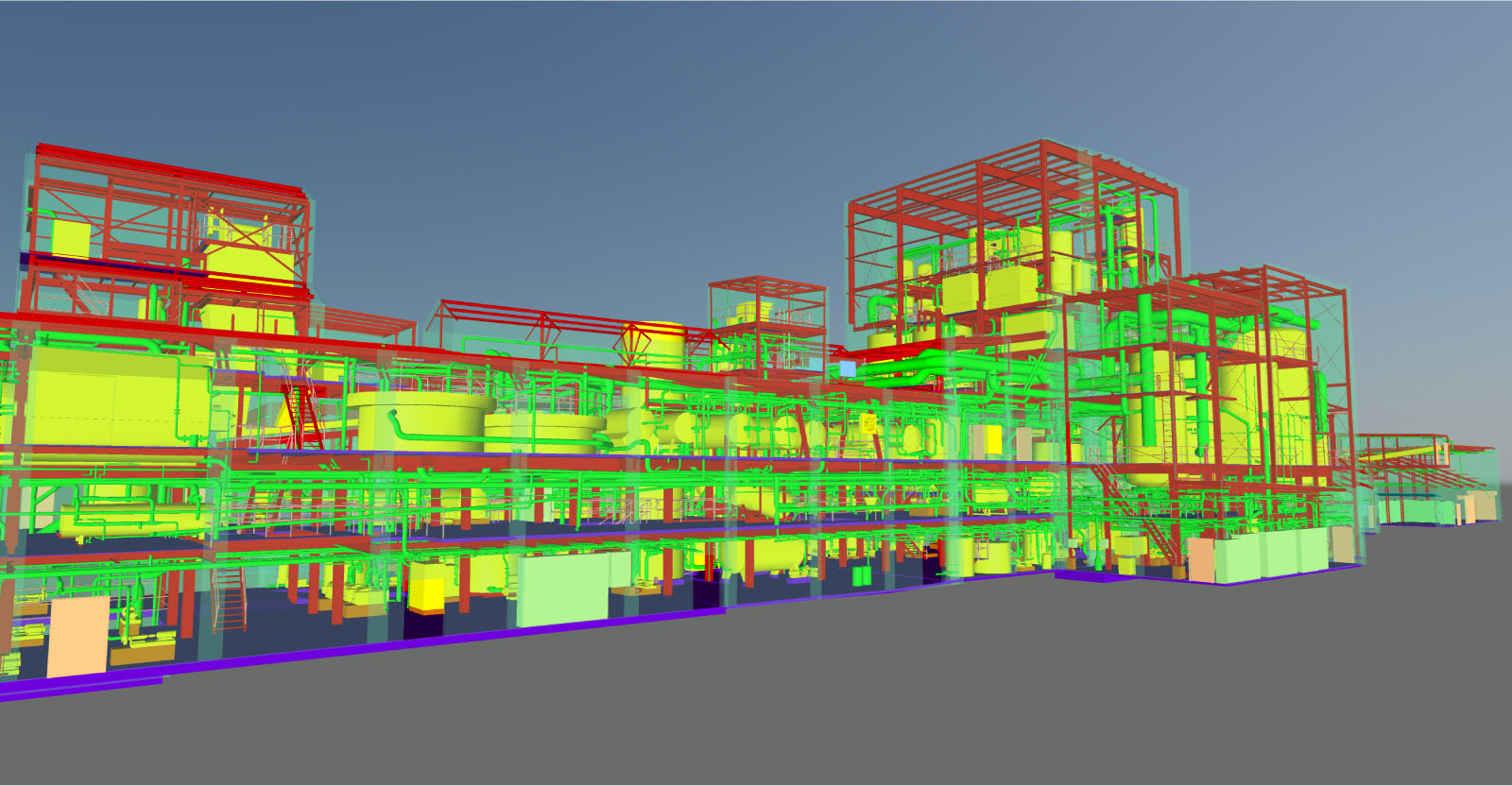
Workflows from the Leica ScanStation laser scanner to Leica Cyclone software were seamless, enabling 3D Imaging Services to register the required elements of the model efficiently and accurately.
Efficient, Accurate Data Capture
In that time [one day], they were able to capture the data from 65 scan positions. James explains, ‘One person could have physically accomplished the job, but we used two to ensure safety.’
Schanbeck wanted to ensure the laser scanned model would provide the level of detail required and would be easy to manipulate. So 3D Imaging Services conducted a pilot project which involved laser scanning for a process equipment retrofit using the Leica ScanStation P40 and creating an as-built model of it. This test application showed that laser scanning was the most efficient, accurate method of capturing the complex conditions of the sugar processing facility.
James explains that they had chosen the Leica ScanStation P40 because of the need to obtain accurate, comprehensive data and transform it into the required as-built model rapidly. By recording everything within its line of sight at a rate of up to one million points per second and producing a point cloud, this laser scanner empowered a crew of two to document the plant in one day. In that time, they were able to capture the data from 65 scan positions. James explains, “One person could have physically accomplished the job, but we used two to ensure safety.”
Also, the ability of the Leica ScanStation P40 to put data into a coordinate system saved time and money because there was no need for a separate crew to carry survey control into the plant from the elevation reference point outside. After the team had established that reference and other reference points throughout the factory, it was easily able to tie the point cloud data to them. Finally, workflows from the scanner to Leica Cyclone software were seamless, enabling 3D Imaging Services to register the required elements of the model efficiently and accurately.
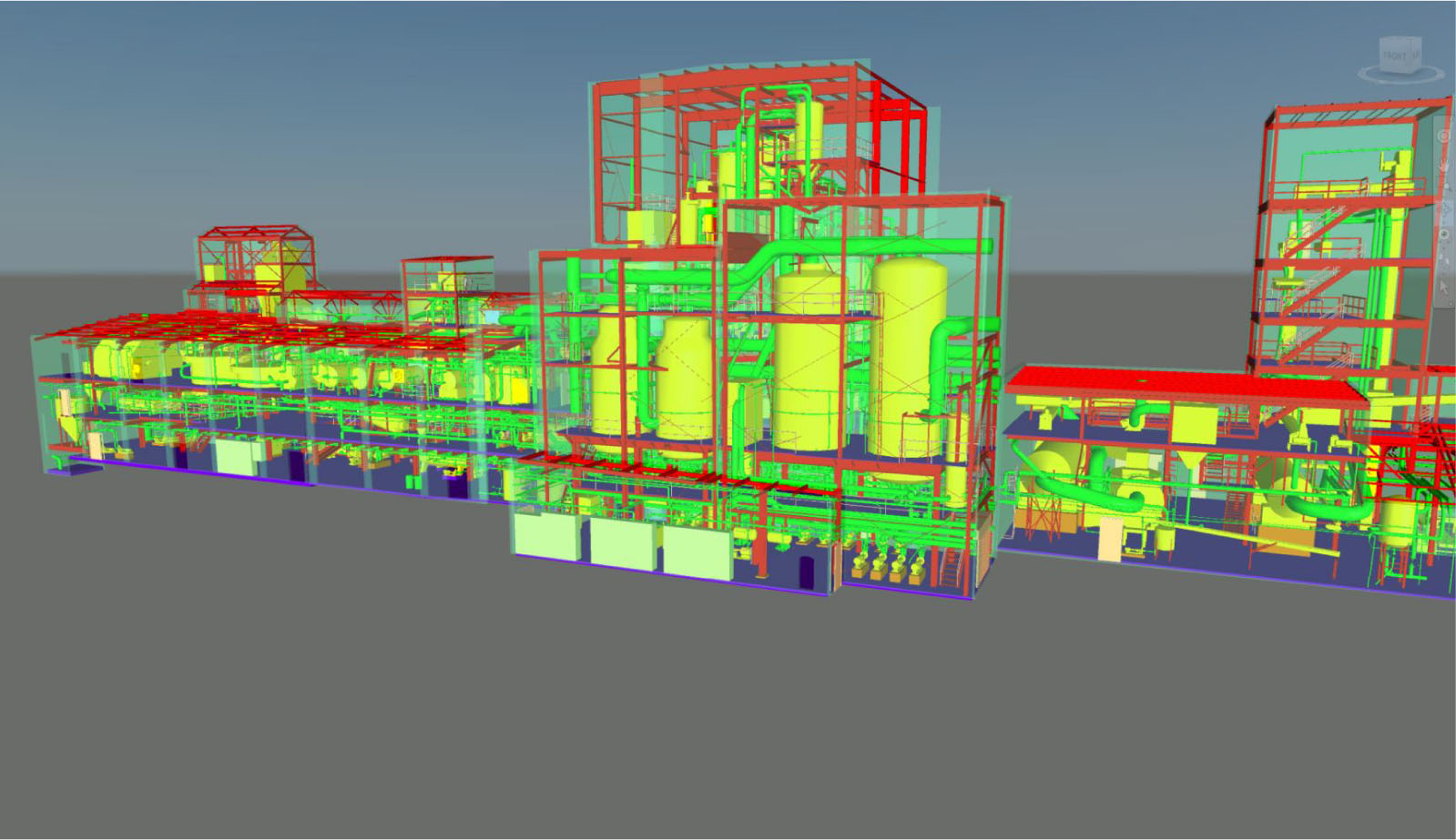
3D point cloud site maps facilitated compressor station installation.
Time and Cost Savings, Plus Better Information
According to James, for the field documentation alone there was a cost savings of 68%.
Without laser scanning, Michigan Sugar would have had to take manual field measurements, and the documentation process would have required almost two weeks to complete. According to James, for the field documentation alone there was a cost savings of 68%. Total savings, of course, go beyond that because manual measurements could have introduced human error, leading to construction clashes and rework. Industry-wide contingencies for rework on plant data gathered manually typically run from 12 to 30% of total project costs, eating up time and money. With the data from the laser scanner, all equipment and systems were captured to within a millimeter of accuracy, not just a few chosen plant elements.
Data processing was also fast and cost effective because the team paired the ScanStation P40 with Leica Cyclone software, which work flawlessly in unison. This marriage of software and hardware made it easy for in-house engineers to extract, analyze the data and create a 3D model in AutoCAD of all architectural, structural and mechanical systems. “Because we controlled all aspects of the project in one software package,” explains James, “we did not have to import and export data from various software packages, saving us a lot of time.”
The survey team also published Leica TruViews, dimensional photographs overlaid on top of the point cloud data, which people can view in Leica Geosystems’ free TruView panoramic viewer. Even though they did not have in-depth knowledge of point cloud software, the professionals at Michigan Sugar were able to review the data and assess site conditions easily with the TruViews. Schanbeck has found the model so useful in helping engineering teams with their design work that he plans to use laser scanning to document the entire facility, facilitating future equipment modifications and additions.
Even though they did not have in-depth knowledge of point cloud software, the professionals at Michigan Sugar were able to review the data and assess site conditions easily with the TruViews.
HIGH-VALUE DELIVERABLES
- High resolution registered point clouds
- Leica TruViews
- 3D CAD models
BENEFITS
Increased Safety
All data captured from ground level
Fast Data Collection
All data captured in a single day with a two-person crew vs. two weeks for a traditional documentation process provided a cost savings of 68%
Comprehensive Data Capture
Accurate, comprehensive data enabled virtual clash checks and prevented rework costs
Better Project Visualization
TruViews and 3D models enable stakeholders to make better decisions