VIS technology that can “see” where it is at each scan position makes it fast and easy for you to capture the as-built data you need to construct a digital twin of your plant.
From the earliest days of capturing hundreds of data points per second, laser scanning has always had tremendous potential for documenting the plant environment. But combining individual scans into one cohesive point cloud remained a challenge. The process was typically performed in the office after the data acquisition was complete, using post-processing software. If operators identified missing data at this stage, they would need to make additional trips back to the plant for more scans.
Company
Any
Location
Any
Juergen Mayer, then business director for terrestrial laser scanning for Leica Geosystems, part of Hexagon, had a different idea. What if the laser scanner could “see” where it was at each scan position? What if the acquired data in the field at each position could be automatically registered with the previous scan data, and the resulting combined point cloud made available in real time on a tablet computer? This would allow the operator to immediately investigate what data was captured and what data was missing, to optimally plan the next scanner setup and, above all, to perform a completeness check while still onsite.
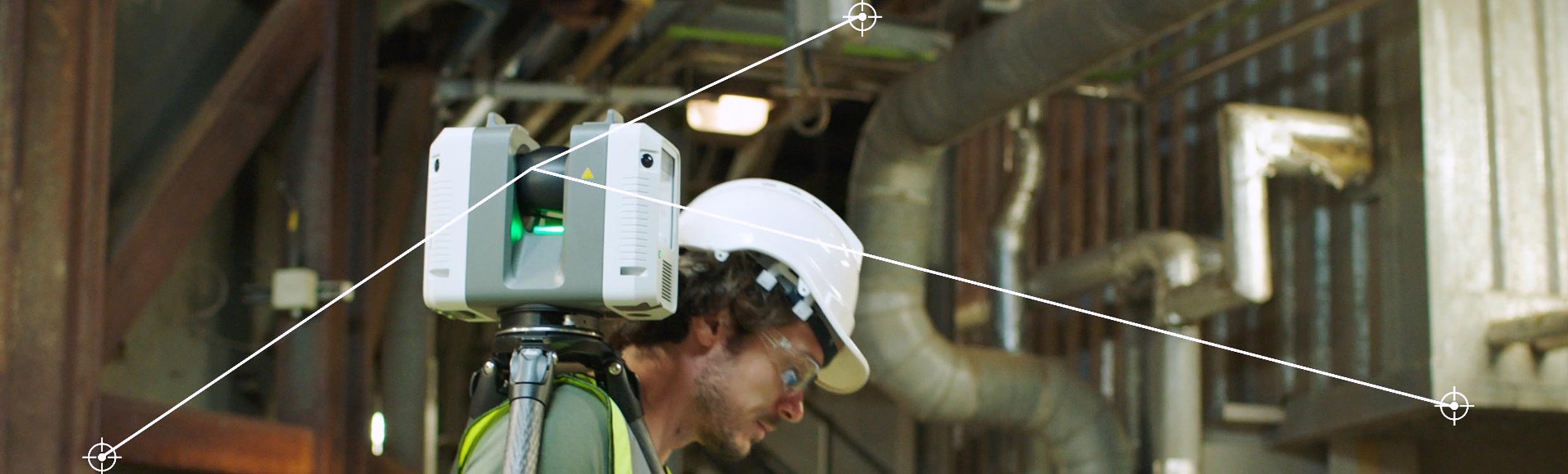
The VIS technology in the Leica RTC360 laser scanner automatically pre-registers data acquired in the field with the previous scan data. The resulting combined point cloud can be accessed on a mobile tablet computer so you can immediately investigate what data is captured and what data is missing, plan the next scanner setup and perform a completeness check while still onsite.
Fast As-Built Data Capture with Instant Insight
With real-time automatic data processing and pre-registration, you can see the results immediately after performing the scan.
This line of thinking led to the Visual Inertial System (VIS) technology in the Leica RTC360 laser scanner. Based on visual simultaneous localization and mapping (SLAM), the VIS algorithm computes the 3D-coordinates (mapping) of tracked features from two or more positions and uses these coordinates to determine the following position (localization). The generated map of landmarks evolves as you move along this track to the next scanner setup and acts as a reference for the whole positioning algorithm. Consequently, the map that is built up and maintained during the process is essential to keep the drift error small. Five cameras built into the laser scanner ensure that the technology will continue to work even if one side of the scanner is obstructed—for example, as you are carrying it. And with real-time automatic data processing and pre-registration, you can see the results immediately after performing the scan.
Duis autem vel eum iriure dolor in hendrerit in vulputate velit esse molestie consequat, vel illum dolore eu feugiat nulla facilisis at vero eros et accumsan et iusto odio dignissim qui blandit praesent luptatum zzril delenit augue duis dolore te feugait nulla facilisi. Lorem ipsum dolor sit amet, cons ectetuer adipiscing elit, sed diam nonummy nibh euismod tincidunt ut laoreet dolore magna aliquam erat volutpat.
The Benefits of VIS on ROI
An Easy Way to Achieve a Digital Twin
There's no easier way to create the foundation for a digital twin of your plant so you can be lean and agile in any environment.
The net result is extremely fast, accurate and comprehensive as-built data collection, captured with a single operator working safely from the ground. With Cyclone FIELD 360 software, data can be shared directly to TruView Cloud for fast and easy collaboration with anyone who needs access, regardless of their device, browser or experience with 3D point clouds. There’s no easier way to create the foundation for a digital twin of your plant so you can be lean and agile in any environment.
If your laser scanner has VIS, that’s a good thing. If it doesn’t, talk to one of our experts to find out how you can put the power of VIS to work for you.